External fire spread is a killer
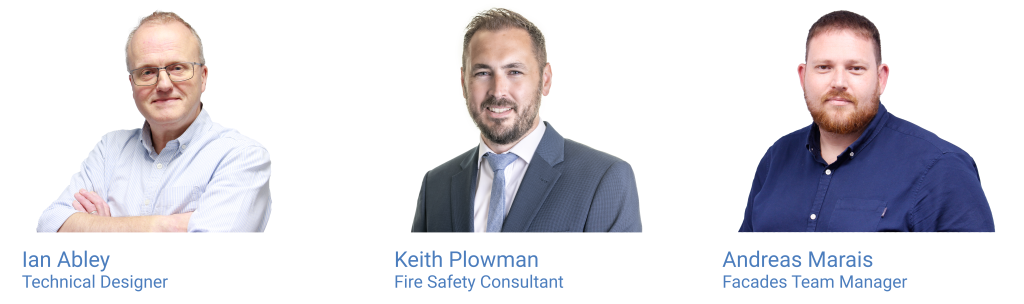
External fire spread is a killer
The Spanish City of Valencia suffered a fatal fire at a pair of large residential apartments on Av. del General Avilés and Av. del Mestre Rodrigo in Campanar on the 22nd of February, 2024. There were 10 fatalities, with many of the residents injured and all made homeless. Windy weather conditions assisted the external wall fire to spread through the combustible Rainscreen cladding, defeating the internal compartmentation. Once again showing the world that external fire spread is deadly.
Seven years ago in London, on the 14th of June, 2017, a now infamous fatal external wall fire started in the early hours of the morning at Grenfell Tower, North Kensington, killing 72 people. Many of the residents were sleeping. The building had been refurbished with combustible ACM cladding with a Polyethylene core called Reynobond, manufactured by Alcoa before they had traded as Arconic. Alcoa had acquired the business of Reynolds.
However, unlike the apartment building in Campanar, the Rainscreen construction at Grenfell Tower was additionally built up with combustible plastic foam insulation of two kinds; mostly foil faced Polyisocyanurate (PIR) insulation manufactured by Celotex, with some areas of foil faced Phenolic Foam (PF) insulation manufactured by Kingspan.
The law of Requirement B4(1) for external fire spread requires:
“The external walls of the building shall adequately resist the spread of fire over the walls and from one building to another, having regard to the height, use and position of the building.”
In the Phase 1 report into Grenfell Tower, Inquiry chairman Martin Moore-Bick said:
“It is apparent from the findings made in earlier chapters that the external walls of the building did not resist, and indeed actively promoted, the spread of fire. That was principally due to the presence of ACM panels with a polyethylene core, but other materials and other features, including the design and geometry of the facade, also played a role.”
What is ACM?
ACM is Aluminium Composite Material, though outside the UK it is often referred to as an Aluminium Composite Panel, or ACP. The composite has facings of thin, precoated aluminium in large format sheets made rigid by a Polyethylene core. ACM is not a thermal insulation material because the composite has a high thermal conductivity. In a built-up Rainscreen the ACM screens the separate thermal insulation product from the rain. Grades of ACM have cores which vary in the amount of fire retardant mineral mixed into the Polyethylene:
- 100% Polyethylene as the “standard” grade product. This is the most concerning type used in the Grenfell Tower refurbishment. Polyethylene burns fiercely, similar to petrol, and in the process melts and burns as a dripping and flowing liquid, spreading fire upwards, sideways, and downwards. The aluminium facings slide off the molten core, and provide no protection against rapid fire spread.
- 30% Polyethylene with 70% mineral as the “fire retardant” grade product, marketed as FR. This does not mean fire resisting. ACM provides no fire resistance, and ACM FR is still combustible. The fire retardant minerals mixed into the Polyethylene core delay and slow the speed of fire spread. That delay, combined with fixing detailing, allows ACM manufacturers to achieve a Class B from European Reaction to Fire tests.
- 10% Polyethylene with 90% mineral as the “limited combustibility” product, often marketed as Class A2. The A2 in European Reaction to Fire classification begins to require calorimetry testing to identify the Gross Calorific Value of the material, as a measure of the fuel it contains for a fire. This A2 type of ACM would require the core to contain less than 3.0 MJ/kg of fuel, which can be compared to 15.0 MJ/kg for softwood, or 45.0 MJ/kg for some “standard” ACM products.
- 5% Polyethylene with 95% mineral products have been developed and marketed since Grenfell Tower fire as Class A1, or less than 2.0 MJ/kg of fuel. This is the lowest possible Polyethylene content, and not in common use.
Therefore, the core material has a direct effect on the combustibility of the ACM panel, which can increase the severity of an external wall fire. As well as this, the detailing of the Rainscreen of ACM panels can contribute to fire behaviour in several ways:
- Fixing methods: Whether ACM panels are riveted as flat sheets to the aluminium support structure bracketed from the backing walls, or folded into “cassettes” and hung off the supports, changes the amount of exposure of the Polyethylene core in the fabrication. It is possible to obtain a better classification with additional rivet fixing in fire tests, or other specific details poorly communicated in test and classification reports, so that some “standard” products have got to market as Class B, though they are 100% Polyethylene.
- Formats of panels: Larger formats present fewer exposed edges at the necessarily open gaps between them to provide ventilation to the cavity in the Rainscreen that protects the thermal insulation on the backing wall. But this is of marginal effect in a real fire situation when cores are melting and the aluminium facings are falling away to expose large areas of combustible Polyethylene.
- Cavities: The ventilation and drainage of the cavity keeps the thermal insulation dry and screened from the rain. However, the cavity in a fire can provide a “chimney effect”, as the fire spreads rapidly upwards through the external wall, attacking the internal face of the ACM and any combustible membranes or thermal insulation fixed to the backing wall. Fire-resisting cavity barriers of stone wool placed at floor levels, at vertical compartment wall lines, and around windows or doors will reduce the “chimney effect”, but are ineffective if the ACM has distorted in the heat, burned away, or fallen off the support structure.
The fire risks associated with ACM cladding were highlighted by the Grenfell Tower fire, which led to the increased scrutiny and regulation of cladding materials.
Correctly identify construction
The Campanar apartment fire was initially reported as a problem of Polyurethane in the external wall construction, repeated by the BBC. However, the fire appeared to be another case of “standard” ACM with a 100% Polyethylene core.
The BBC corrected reporting on the Campanar fire to recognise Polyethylene. The BBC had referred to Google Maps Street View, scrolled back to 2008, showing the external wall under construction. Although the graphics were upside down, the temporary peel-off protective sheets clearly featured a Larson brand logo, as the range of ACM manufactured by Alucoil.
Better images showing the external wall Rainscreen built-up with stone wool insulation circulated on LinkedIn. The Campanar apartments had non-combustible insulation, but combustible ACM cladding with a Polyethylene core. It will take forensic investigation to precisely identify the specification and detailing of the external wall.
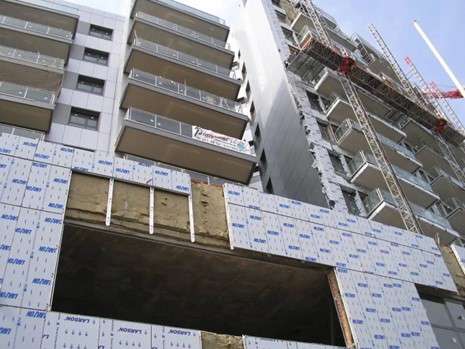
Correct identification of the ACM product matters as it does for any specification and detailing of external wall construction. The Fire Protection Association (FPA) campaigned for their 75-year anniversary with the sensible advice “Know Your Building”.
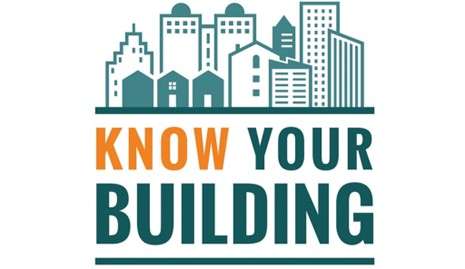
Governments, as much as building owners and their insurers, are realising there are problems for fire safety with a few types of external wall construction. This technical realisation is growing not only in devolved administrations of the UK but across the nations of Europe and to wider markets.
The risk of deadly and harmful fires involving external walls is a concern for many Authorities Having Jurisdiction (AHJ), often resulting in overlapping responsibilities among the authors of technical standards.
British standards have long been specified in Commonwealth countries or transposed as international alternatives. European standards were considered optional in the UK statutory guidance to Schedule 1 Requirements of the Building Regulations 2010, before and after Brexit from the European Union.
Registration of buildings with defective external wall construction
The LFB (London Fire Brigade), along with all other Fire and Rescue Services in England and Wales, may do more than issue Alteration Notices or Enforcement Notices. To issue a Prohibition Notice under Article 31 of the Regulatory Reform (Fire Safety) Order 2005 means prohibiting useful occupation * of a building to ensure people’s health and life safety. Article 31 of the RR(FS)O 2005 is the greatest power that can be exercised by any Fire and Rescue Service in England and Wales.
*31.—(1) If the enforcing authority is of the opinion that use of premises involves or will involve a risk to relevant persons so serious that use of the premises ought to be prohibited or restricted, the authority may serve on the responsible person or any other person mentioned in article 5(3) a notice (in this Order referred to as “a prohibition notice”).
Before Grenfell Tower fire the National Fire Chiefs Council (NFCC), representing the whole of the UK, maintained an Enforcement Register of published Notices. However, not all Fire and Rescue Services use the NFCC service.
The London Fire Brigade does not provide information about their Notices through the National Fire Chiefs Council service, and the regional information from those who contribute may be partial and out of date, as there is no legal duty to compile the NFCC register. Also, the NFCC register data cannot be readily accessed, and information is poorly categorised. Therefore, it is not possible to identify the buildings that have been notified by Fire and Rescue Services for a breach of B4(1) in England, or to get a sense of the wider UK.
The state is discovering through the newly created Building Safety Regulator (BSR) at the Health and Safety Executive (HSE) where Higher-Risk Buildings (HRBs) are located.
Under Section 65 of the Building Safety Act 2022 an HRB has at least two units of residential accommodation and is either 7 storeys or more than 18m in height. That is not the overall building height, but rather the upper occupied storey height over 18m above ground as Regulation 5(1) of the additional Higher-Risk Buildings (Descriptions and Supplementary Provisions) Regulations 2023. This legislation also explains differences with the Higher-Risk Building definition in Section 120D of the Building Act 1984, however definitions may better align over time.
Owners of an HRB, under the criteria in the Building Safety Act 2022, must appoint “Accountable Persons ” as individuals or organisations to be responsible for the safety of the common parts of the building used by residents, including external walls and roofs. The named Principal Accountable Person (PAP) registers the HRB with the BSR, and updates the register of information with all changes during building occupation. Online, some HSE guidance talks more generally of “high-rise”, but they mean an HRB. The Higher-Risk Buildings (Keeping and Provision of Information etc.) (England) Regulations 2024 apply.
The HSE provide an HRB Register, searchable by Post Code, that identifies the PAP. It is not possible to publicly obtain a copy of the full BSR register of HRBs or access the information in its entirety.
According to the Institution of Structural Engineers, there is a legacy of 12,500 HRBs registered with the BSR at the HSE, but not all of these will have defective external walls in need of remediation. The 2000 new HRBs added to that stock each year should be without defects.
However, there is no obvious register of the larger additional number of non-HRBs that have external walls known by the Fire and Rescue Service to be in breach of B4(1) in England.
Assuming that a technical overview of external wall typologies exists at the BSR, there is no HSE-authorised categorisation of defective construction in breach of B4(1) that could be used to compile a register for the stock of buildings in sleeping risk residential Purpose Group 1a, or other Purpose Groups in the statutory guidance of Approved Document Part B.
AD-B Volume 1 Dwellings
1a Flats (which includes all BSR registered HRBs)
1b Dwellinghouse with a storey over 4.5m above ground
1c Dwellinghouse with a storey under 4.5m above ground
AD-B Volume 2 Buildings other than Dwellings
2a Institutional Residential, such as a hospital, home, school or other similar establishment, where people sleep
2b Other Residential, such as a hotel, boarding house, college, hall of residence, hostel or any other residential purpose
3 Offices
4 Shop and Commercial
5 Place of Assembly, Entertainment or Recreation
6 Industrial Factories
7a Storage and other non-residential buildings
7b Car parks designed to admit and accommodate only cars, motorcycles and passenger or light goods vehicles that weigh a maximum of 2500kg
In England and Wales, fire safety responsibilities for all buildings that are not HRBs are defined under the Regulatory Reform (Fire Safety) Order 2005. This legislation designates specific individuals and organisations as “Responsible Persons,” tasked with overseeing and maintaining fire safety within their buildings. This responsibility applies to all workplaces and the common parts of buildings containing two or more domestic premises.
The scope of what constitutes “common parts” of buildings was confirmed by the Fire Safety Act 2021, explicitly including external walls and roofs, which was not a change in meaning from the Regulatory Reform (Fire Safety) Order 2005. This confirmation highlighted the need for a comprehensive approach to managing potential fire risks associated with the building structure via external wall inspections; an acknowledgement of the risks posed by external wall constructions following a number of significant fire incidents.
Other measures depend on preventing a rapidly spreading external wall fire
The external wall fire at Campanar, much like the tragic Grenfell Tower incident, starkly reminds us that fires originating or spreading via external walls can undermine the internal compartmentation designed to safeguard escape routes. Building Regulations Schedule 1 Requirements B4(1) for the external wall and B4(2) for roofs are crucial as they support the broader suite of fire safety measures—from B1 to B5. Collectively, these requirements must be addressed in a coherent fire strategy to protect building occupants. When a fire spreads through and over external walls and roofs, it often bypasses internal protections, directly threatening the lives of occupants and the integrity of the entire fire safety system.
There is a stock of residential buildings in the UK with external wall construction that breach legal Requirement B4(1). Their identification before a fatal or injurious fire is important.
The London Fire Brigade (LFB) have stated that they are concerned with 1,250 high-rise residential buildings in London alone. Commissioner Andy Roe has often called for action on remediation works. Although, pleas to “do the right thing” are technically undefined, given the vagueness of B4(1).
The “right thing” for the external wall is shown on the right-hand or “restricted” side of the Second Edition Figure 2, 2003, and Third Edition Figure 3, 2013, of BRE, BR 135 Fire performance of external thermal insulation for walls of multistorey buildings.
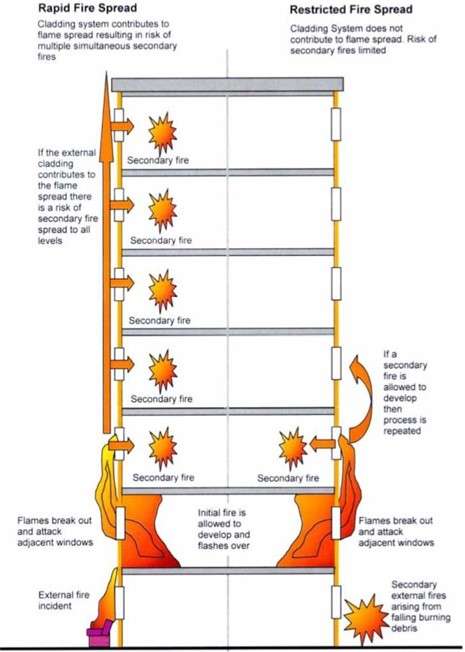
Occupation denied under B4(1)
An external wall that is physically incapable of supporting rapid fire spread in any condition should be the precondition of occupancy. The decision to deny occupancy is a critical moment at Handover, as Work Stage 6 in the RIBA Plan of Work 2020.
The Fire and Rescue Service are authorised to deny occupancy after it has occurred under the RR(FS)O 2005, clarified by the Fire Safety Act 2021. Often Regulation 38 has been ignored. Fire safety information at Handover should include calorimetry for the external wall construction. A “Responsible Person” should have that basic information, with Regulation 38 now listed in both Volumes of Approved Document Part B (2019 as amended 2020 and 2022).
For which the insurance sector has provided an annotated version of Volume 1 Dwellings, and Volume 2 Buildings other than Dwellings that relate to BDM01 A to Z of Essential Principles for the protection of buildings.
The Building Safety Regulator (BSR) has the power to deny occupancy at Gateway 3 for “Higher-Risk Buildings” under the Building Safety Act 2022, even though the new staff at the Health and Safety Executive (HSE) have overall responsibility for the entire Building Control profession. An “Accountable Person” should have collected the basic calorimetry.
The advice “Know Your Building” should involve knowing the Gross Calorific Value of the materials from which the external wall is already built, or going to be built, by using simple samples for calorimetry; meaning strategic decisions can be made.
It is fortunate, after fatal fires at Grenfell Tower in London and the Campanar apartments in Valencia, that there have not been more fatal fires in occupied buildings with combustible external walls.
La suerte no es una estrategia de fuego…
Luck isn’t a fire strategy…
To discuss the contents of this article, or your building needs, contact a member of the team.